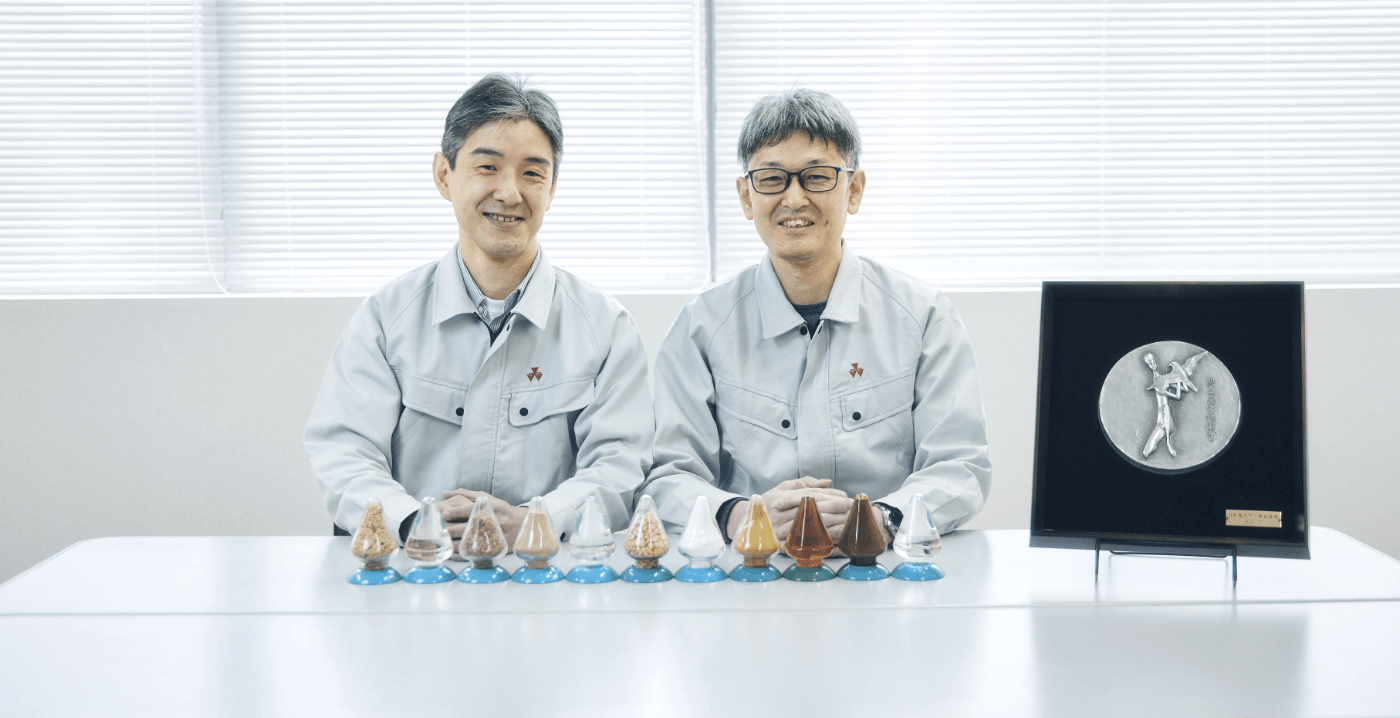
PROJECTSTORY#2
1枚の企画書が社の命運を背負った大プロジェクトに。
イノベーションを起こした「フィットファイバー」開発
PROJECT
MEMBER
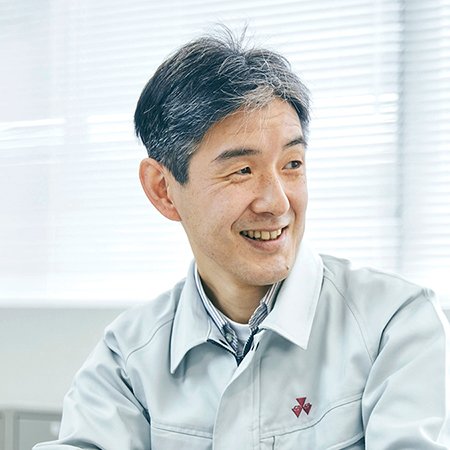
N・H
研究所
技術営業課所属
2003年度入社、研究所研究一課に配属。当初は酵素生産菌の育種等を担当していたが、2009年にテーマコンペで提案した企画が採択され、フィットファイバーの研究開発に従事する。
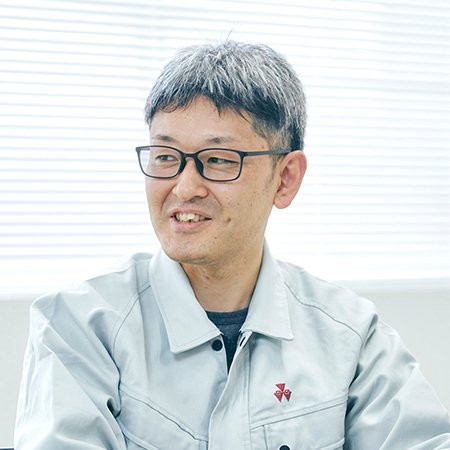
S・T
富士本社
技術部所属
2003年度入社。工務部、技術部で設備の更新、改善工事の計画、実行管理に携わる。本プロジェクトでは実機製造技術統括、実機プロセス案・パイロット設備案の検討などを担当。
未病に寄与する当社の象徴的製品である「フィットファイバー#80」は、難消化性グルカン(水溶性食物繊維)を主成分とし、活性炭触媒による糖重合という画期的な技術によって生まれた自然な味質を有する製品です。製品化のきっかけは一人の若手研究員のコンペでの提案でした。全社的プロジェクトにおいて、研究と設備設計の中核として活躍した同期入社の2名が、提案から市場に送り出すまでの苦労と成功体験を語ります。
01若手にも平等にチャンスが与えられる「テーマコンペ」。
N・H当社には研究所所員を対象にした「研究テーマコンペ」という機会があり、このコンペでは研究職員のアイデアを直接経営層に提案できます。私は入社6年目の2009年、当時研究所の目標のひとつであった難消化性糖質の開発に自らのアイデアが寄与できればと考え、固相反応による糖ポリマー製造技術の提案をしました。運も味方したのでしょうが、なんとか採択され、1年間自由に検討する時間と予算を頂くことになりました。これがフィットファイバー開発の始まりでしたね。
続く2010年のテーマコンペでは、苦難の連続だった1年目の研究をベースに実用化をアピール。「食物繊維素材の開発」として再提案しました。実現性のあるビジネスを意識したプレゼンだったこともあり、翌年4月にはプロジェクトチームが発足。その後は、製品化に向けての歯車が一気に加速するように回り出しました。とはいえ、ビジネスとして成立させるには、ここからさらに幾重もの難関を乗り越える必要がありました。そのためには信頼できるチーム、パートナーが必須でした。このチーム(プロジェクト)でめぐり合ったのがS・Tさんです。
S・T私はプロジェクトチーム発足の段階で設備担当として参画しました。それまで携わってきた既存設備更新業務から、まったく新しい製品開発に関われるとあって、ワクワクしましたね。社内の期待の大きさを感じていたので「なんとか製品化までもっていくぞ!」と決意したことを覚えています。
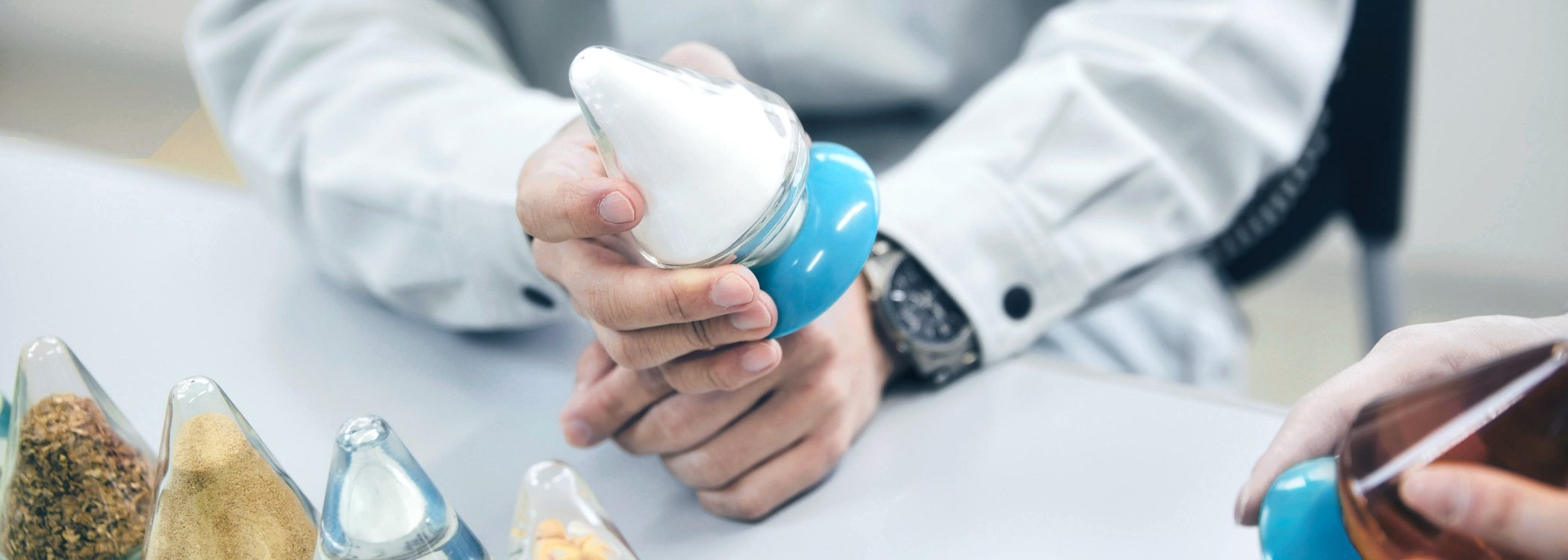
02製品化まではトライアンドエラーの連続だった。
N・Hプロジェクト発足後は、研究所のリーダーとして社内のさまざまなセクションと折衝し、製品化プロセスを進めることが私の役目でした。会社から要求される納期も短く、スピードが要求されたので課題進捗管理が大変キツかったですね。研究していた時も壁を感じることは多かったのですが、特に「設備選定と安定運転」「原料や触媒等、製造条件の最適化」「食物繊維含量の担保」といったいくつもの課題に苦戦を強いられました。ラボスケールで検討を重ね、2012年秋に完成したパイロットプラントでの検討後、最後に二十数バッチの実機製造試験を経て製品化につなげていきましたが、設備選定から安定稼働まで、ずっとトライアンドエラーをしていました。S・Tさんの技術部とは非常に多くのやり取りを重ねましたね。
S・Tそうですね、今まで扱ったことのない製品だったので、前例がなく、どのような機械でつくれば良いのかということから考えました。研究所や協力業者とさまざまな機械によるテストを繰り返し、製造方法の目途を立てていきました。小規模のラボスケールでうまくいったとしても、そのままではビジネスにはなりません。でも、機械の規模をビジネスが可能なレベルまで上げると、途端に不具合が起こる。製造スケールを大きくしていくことの難しさを痛感しましたね。
自社内にパイロット設備、プラント設備を建設してからは毎月6日間、24時間体制での運転となり、夜間でもトラブル発生の電話が鳴らないか不安でした。さまざまな社内のプロフェッショナルの知恵や経験を借りながらトラブルをひとつひとつ潰し、軌道に乗せていったと思います。試作を繰り返すうちにメンバーのスキルが上がるなど、多くの部署の方とともに製品化という大きな目標に向かって突き進みましたね。莫大な予算を設備に投じるわけですから、技術部としては、その重圧感を強く感じていたと思います。
N・H運転条件を確立するまで、改良とテストの連続で経験値を積み上げて解決していった感じですよね。いつ止まるかわからない設備で昼夜連続運転を何度も試みるなど、当時の技術メンバーは体を張って対応してくれたと思います。本当に感謝してもし切れません。
今にして思えば、私とS・Tさんが同期入社だった、ということが功を奏した気がします。一緒に仕事をするのは、このプロジェクトが初めてでしたが、社内研修から一緒だったので、非常にやりやすかったです。出張含め過ごす時間が長かったので、あらゆる話をしましたよね。このコンビでなければうまくいかなかったことも多かったのではないか、と今になって思います。
S・T3時間以上の移動やホテル生活など、慣れない環境で苦労もありましたが、N・Hさんとの移動中の会話は、私にとっても楽しみのひとつでした。そこで、研究者としてのさまざまな考え方を教えてもらいました。天才的な発想ありきの研究なのかと思いきや、入念な下調べをしながら研究されていることに感銘を受けましたね。
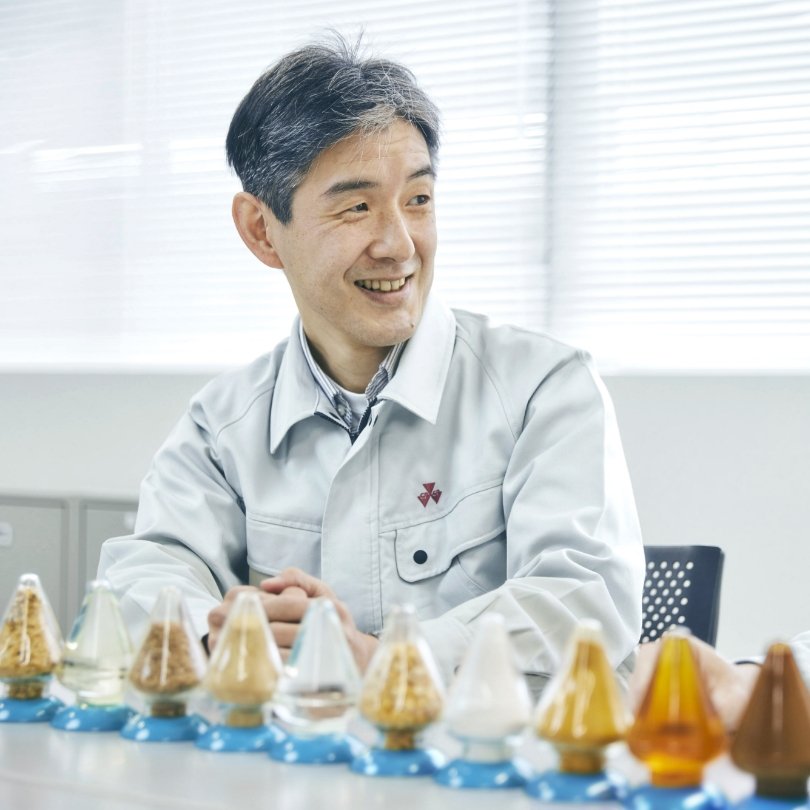
03常にイノベーションを生み出せる組織をつくっていく。
N・Hそして、2014年6月にフィットファイバーは製品化となりました。低糖質・低カロリーに寄与することや、生理機能として整腸効果・血糖上昇抑制効果もあり、今では幅広い飲食品に使用いただいております。摂取不足となっている食物繊維を取りたい、お通じや血糖のケアをしたい、カロリーや糖質を抑えたいといった健康ニーズに応える食品素材です。私は現在も利用開発を通して、拡販ツールの拡充やフィットファイバーシリーズの拡販や営業支援を行っています。
S・T水溶性食物繊維という素材自体は以前からあるもので、市場では認知されたものです。しかし、フィットファイバーはその特徴的な製法から低コスト製造が可能で、競合製品の中でも、安価で安全な製品というところに価値があります。それに加え、フィットファイバーの主要生産設備は国産機器で構成されています。それも安全・安定供給に貢献できている部分だと思います。私からするとN・Hさんがテーマコンペに応募してなかったらこの成果は体験できなかったわけですから、本当に感謝していますよ。
N・HこちらこそS・Tさんはじめ多くの人たちへの感謝ばかりです。ソフトハード両面での莫大な予算も諸先輩の調整力があったからこそ承認されたものですし、事業化につながった大きな要因の一つです。今後はフィットファイバーの研究開発を通して得た経験やスキルを活かして、新たな素材開発や人材育成に携われればと思っています。
S・T当社は多種多様な食品素材、工業素材を製造しているメーカーで、今後も持続して製品を供給していく責任があると思っています。また、今後も新しい製品が開発されたり、生産数量が変化したりするなど、さまざまな環境変化が起きるでしょうから、それに合わせて生産設備も進化していく必要があります。工場の持続とともにそのような変化に対応するため、常に効率的で先進的な工場設備であるよう職務を果たしていきたいです。夢は新工場の建設です。
N・Hいいですね。会社の未来の姿として、他の追随を許さない技術力の構築と、組織として「イノベーション」を生み出せる企業として成長していければ良いですよね。アイデアを創出しリーダーとして挑戦する人、その挑戦をさまざまな形で支援する人、それぞれがリスペクトしながら働けるような姿にしていければと思います。
フィットファイバーは構想から約5年で製品化しており、開発速度はかなり速い方だと思います。素材を見いだして市場に投入するまでには時間がかかるので、入社10年以内の若手に活躍してもらいたいです。糖化製品を取り巻く環境は厳しい状況です。ですからイノベーションの創出が必要であり、そのためには若い時に挑戦して経験を積んでほしい。時代背景や新しい技術を取り入れつつ、局面を変えるようなストーリーの提案に期待しています。
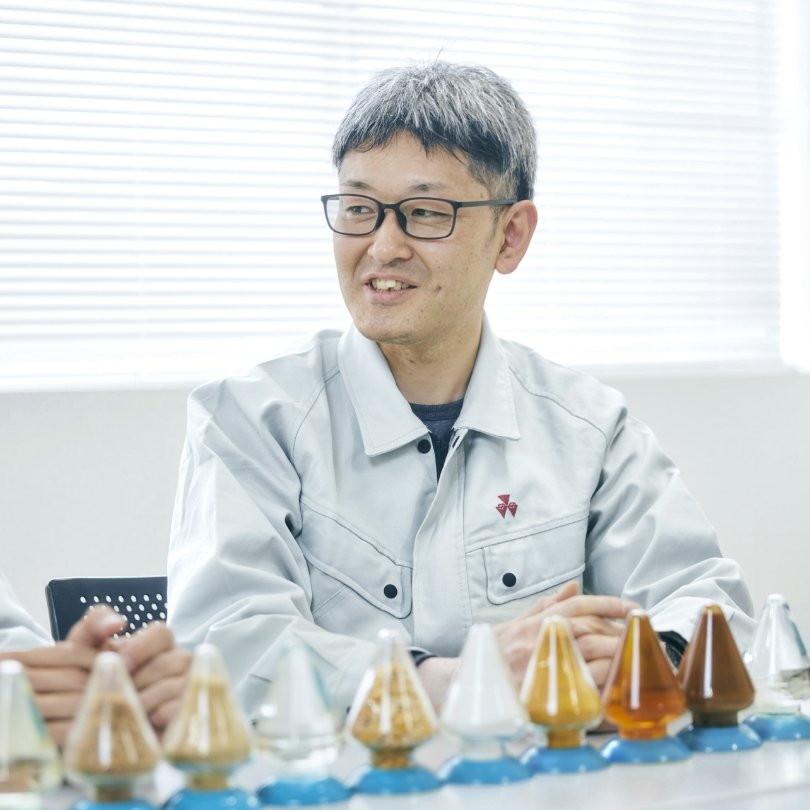
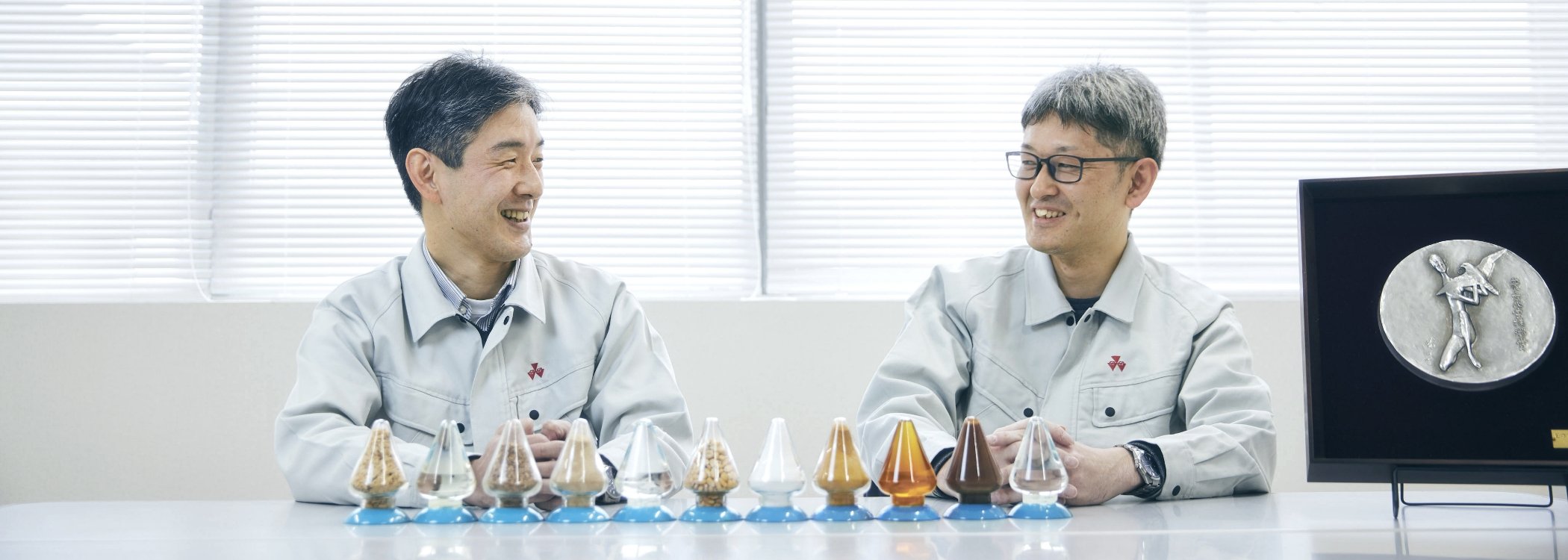